Town of Newburgh, Wastewater Treatment Utility
Fats, Oils and Grease Discharge Permit
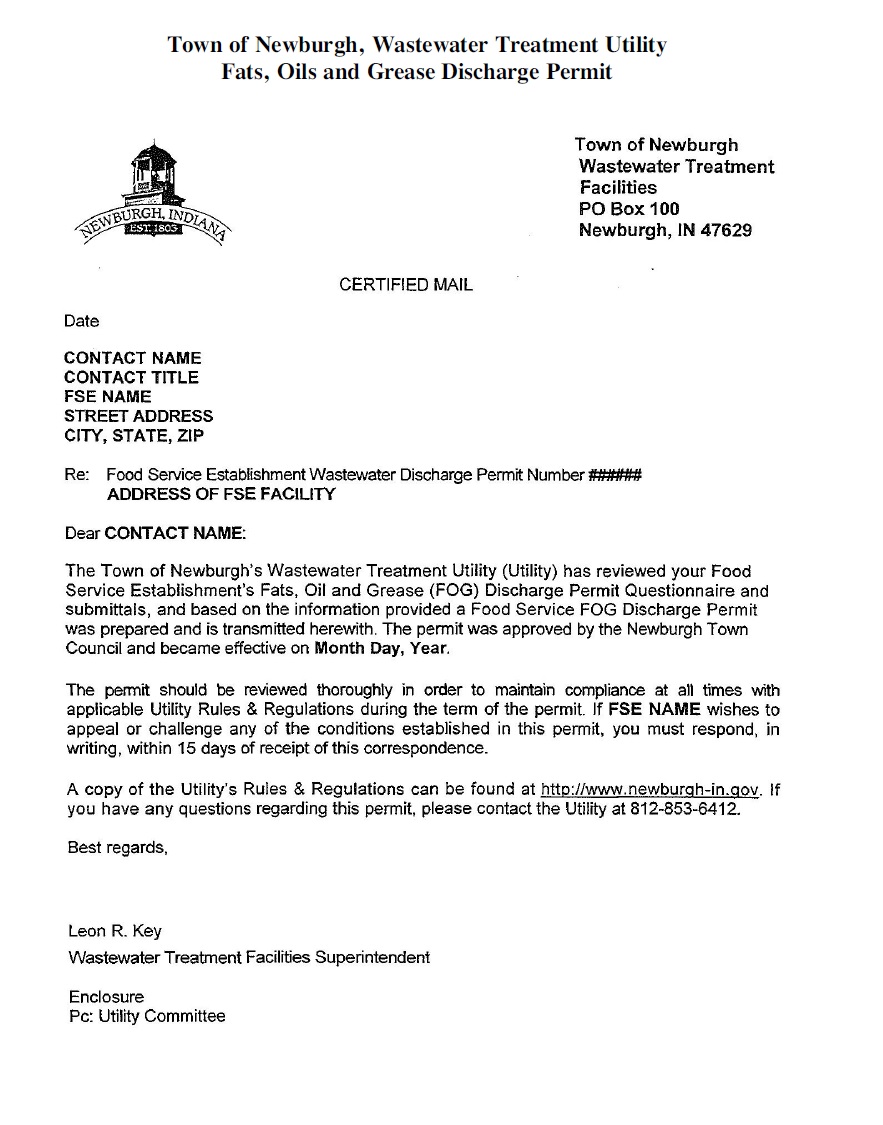
Town of Newburgh
Wastewater Treatment Utility
Food Service Discharge Permit
Wastewater Treatment Utility
Food Service Discharge Permit
Permit #: Effective Date: |
In accordance with all of the terms and conditions of the Rules and Regulations and Policies of the Town of Newburgh (Town) and any applicable provisions of Federal and/or State law or regulation, permission is hereby granted to: FSE NAME located at FSE FACILITY ADDRESS to discharge non-domestic wastewater into the Town of Newburgh’s sanitary sewer system. This permit is granted in accordance with the Food Service Establishment Wastewater Discharge Permit Questionnaire and in conformity with plans, specifications and other data submitted, all of which are filed with and considered as part of this permit. |
Wastewater Treatment Facilities Superintendent |
THE PERMIT MAY BE REVOKED: |
a) If applicable fees or fines are not paid within thirty (30) days of the due date; |
b) If the nature of the discharge changes; |
c) If ownership is transferred without prior approval of permit transfer; |
d) If town, state and/or federal rules and regulations change; |
e) If false information or data is/was given; or |
f) If a violation of the permit occurs. |
(A) General requirements and regulations.
(1) All discharges containing grease and oil must pass through grease control equipment (GCE) before entering the sanitary sewer. GCE refers to any equipment that removes fats, oils and grease from wastewater such as a grease trap which is installed inside the building usually under a counter/sink or built into the floor of the kitchen area; or a grease interceptor which is usually installed outside in the ground and is much larger in size. GCE must be well-maintained and in proper operating condition at all times.
(2) All discharges into the sanitary sewer system are subject to the conditions of this permit and the town rules and regulations.
(3) The town reserves the right to re-open the permit to establish more stringent limitations or requirements on discharges to the wastewater sanitary sewer system or change any other permit condition deemed necessary.
(4) The conditions of this FOG permit shall remain in effect indefinitely, unless the town chooses to discontinue or revoke this permit. Should the town choose to discontinue or revoke this permit, an official letter of notification will be sent expressing the town’s intentions.
(5) Should your GCE be deemed insufficient or in need of repair, the town may require additional GCE to be installed or require the existing GCE to be repaired or modified to meet the original design specifications.
(6) Should new GCE be installed or existing GCE be replaced, the new GCE must meet all current town design criteria and be pre-approved by the town.
(7) Use of additives (including enzymes and biological) are prohibited in plumbing tied into GCE unless express written permission is received from the town. In no case shall the use of a town approved additive extend the required cleaning frequency of the GCE.
(B) Grease control equipment requirements. Permit writer should list the required GCE: grease interceptors; under-counter or in-floor grease traps; waste oil collection devices; or other applicable pretreatment units shall be installed, operated, maintained and repaired solely at the customer’s expense.
(C) Schedule for compliance with the FOG discharge policy. (Permit writer: choose one or more of the following):
(1) New food service establishment (FSE): a grease interceptor shall be installed, inspected and approved by the town wastewater treatment utility (utility) before commencing any wastewater discharges to the sanitary sewer system.
(2) Existing FSE without an existing grease interceptor: a grease interceptor shall be installed, inspected and approved by the town wastewater treatment utility (utility), and the FSE must be in full compliance with its food service discharge permit within six months of issuance.
(3) Existing FSE with an existing grease interceptor and found to be in noncompliance with the FOG policy: staff will need to evaluate the information contained in the permit application to determine if the existing GCE is adequately sized or if failure of the GCE is due to improper maintenance.
(4) Existing FSE being renovated or expanded:
(a) A grease interceptor shall be installed, inspected and approved by the town wastewater treatment utility (utility), and the FSE must be in full compliance with its food service discharge permit within six months of issuance; and
(b) FSE being renovated or expanded that already has a FOG discharge permit: staff will need to evaluate the information contained in a new permit application to determine if the existing GCE is adequately sized and if permit modification is necessary.
(5) FSE receiving a waiver or exemption from the installation of a grease interceptor: staff will evaluate the information contained in the permit application to determine if internal grease traps are required.
(D) GCE servicing requirements.
(1) All GCE shall be maintained by the owner at his, her or its expense and functioning efficiently at all times.
(2) Your facility must have a contract with a GCE “cleaning service company/hauler” unless the GCE is cleaned by your own employees. If the GCE is cleaned by your own employees, then a cleaning log and a cleaning schedule must be maintained to record all cleanings and the final disposal destination of the removed grease. If an outside company performs the cleaning of the GCE a hauling manifest/receipt must state the final disposal destination of the grease removed from the GCE. All material removed from GCE must be disposed of properly by being removed from the property and not discharged to the sanitary sewer system.
(a) Interior GCE - “grease traps”.
1. Interior GCE must be cleaned as needed to operate effectively. In no case shall the cleaning frequency be less than every seven days, unless permission has been given by the utility to extend the frequency based on the actual usage.
2. Interior GCE must have a “flow restrictor” installed to control the volume of flow entering the GCE. This flow restrictor must be in place and in proper working order at all times. The flow restrictor may be mounted in the wastewater drain pipe flowing toward the GCE or it may be built into the design of the GCE, depending on the type of GCE that is installed. The flow restrictor must be inspected at a minimum of once per year to ensure the restrictor is still in place and restrictor orifice has not been altered or has not deteriorated. The permittee must record and document this inspection in his, her or its on-site maintenance log.
(b) Exterior GCE - “grease interceptors”.
1. The exterior in-ground GCE cleaning frequency shall not be less than every 90 days between cleaning unless permission has been given by the town to extend the frequency based on the actual usage.
2. GCE must be pumped out completely (total pump), and no water from the GCE will be discharged back into the GCE after the pumping is completed unless prior approval is given by the town. The GCE should be filled with “fresh water” after the total pump.
(E) Best management practices. The FSE shall comply with the following best management practices (BMPs).
(1) BMPs to prevent blockages in the sanitary sewer.
(a) Educate employees on the BMPs and the importance of preventing fats, oils and grease from entering the sanitary sewer system.
(b) Dispose of food waste by recycling and/or solid waste removal.
(c) Dry wipe pots, pans and dishware prior to washing.
(d) Use absorbent pads to soak up fats, oils and grease under fryer baskets.
(e) Post “No Grease” signs above sinks and in front of dishwashers.
(f) Properly dispose of all fats, oils and grease into recycling containers. No FOG should be poured into a drain or flushed into sanitary sewer collection system.
(g) Place covers on containers before transporting used oil and grease to recycling containers.
(h) Recycle FOG waste via rendering or recycling companies.
(i) Collect and recycle used cooking oil in appropriate containers for recycling.
(2) BMPs to properly maintain grease traps and interceptors.
(a) Observe proper grease interceptor cleaning and maintenance procedures to ensure that the device is operating properly. Regular and proper service maximizes interceptor efficiency, prevents spills and minimizes odor.
(b) Train all staff to regularly check the depth of solids and thickness of retained FOG in the grease interceptor. As a general rule, an interceptor loses its effectiveness when excessive amount of FOG and/or solids accumulate. The frequency of servicing is determined by the accumulation rate of FOG and solids.
(c) Service the grease interceptor at regularly scheduled intervals. Have a licensed and certified hauling, rendering or pumping company clean, pump down and service the grease interceptor regularly.
(d) Witness all grease trap or interceptor cleaning and maintenance activities to ensure the grease control device is properly cleaned and is operating correctly.
(e) 1. Clean under-sink, under-counter or in-the-floor grease traps weekly. These grease traps have less volume than grease interceptors. Weekly cleaning of grease traps by the establishment’s own maintenance staff will reduce the cost of cleaning the grease interceptor.
2. If the establishment does not have a grease interceptor, the grease trap is the only means of preventing grease from entering the sanitary sewer system. If the grease trap is not providing adequate protection, the utility will require the installation of a grease interceptor.
(f) Keep a maintenance log. The maintenance log serves as a record of the frequency and volume of cleaning of the grease trap/interceptor. It is required by the FOG policy to ensure that maintenance is performed on a regular basis.
(F) Record keeping.
(1) (a) The “FOG Folder” must be kept at FSE facility address. This folder shall be available for periodic inspections, including copying by the town.
(b) This folder must contain the following records at all times:
1. The food service discharge permit;
2. Completed interior GCE cleaning logs and cleaning schedule (including receipts from cleanings performed by outside companies);
3. GCE maintenance and inspection logs and all calibration records for instrumentation and flow meters;
4. Copies of all receipts and hauling manifests for exterior GCE cleanings. The FSE must obtain the final disposal copy of the hauling manifest showing where the final disposal occurred;
5. Copy of the contract/agreement with the GCE cleaning company/hauler;
6. Specifications on all GCE being used at the facility; and
7. Any correspondence including past notices of violation from the town.
(2) All records shall be retained for a minimum of three years.
(3) Failure to meet any of the record keeping requirements is a violation of the food service discharge permit and the town’s rules and regulations.
(G) Right to inspect. The utility shall have the right to enter the premises of any establishment to determine whether the establishment is complying with all requirements of the FOG policy, with any wastewater discharge permit or with any order issued by the utility. FSEs shall allow the utility ready access to all parts of the premises for the purposes of inspection, sampling, records examination and copying, and the performance of any additional duties during reasonable business hours.
(1) Where an establishment has security measures in force, which require proper identification and clearance before entry into its premises, the establishment shall make necessary arrangements with security so that, upon presentation of suitable identification, utility staff will be permitted to enter immediately for the purposes of performing specific responsibilities.
(2) The utility shall have the right to set up on the establishment property, or require installation of, such devices and/or structures as are necessary to conduct sampling and/or metering of the establishment’s operations.
(3) The utility may require the establishment to install monitoring equipment as necessary. The establishment’s sampling and monitoring equipment shall be maintained at all times in a safe and proper operating condition by the establishment at the establishments expense. All devices used to measure wastewater flow and quality shall be calibrated at least annually to ensure accuracy.
(4) Any temporary or permanent obstruction to safe and easy access to the establishment’s FOG control devices, interceptors or equipment to be inspected and/or sampled shall be promptly removed by the establishment at the written or verbal request of utility staff and shall not be replaced.
(5) Unreasonable delays in allowing utility staff to access the establishment’s premises shall be a violation of this permit.
(H) Permit violations. No permittee shall discharge wastewater to the sanitary sewer system in violation of the FOG policy or the utility’s pretreatment discharge limitations.
(1) It shall be a violation of the permit for any permittee to:
(a) Modify a grease interceptor structure without the consent or approval of the utility including alteration or removal of any flow constricting devices so as to cause flow to rise above the design capacity of the grease interceptor;
(b) Provide false maintenance records;
(c) Cause or permit the plugging, blocking or interference with a grease interceptor or permits others to cause such interference; and
(d) Failure to comply with the provisions of a FOG discharge permit or the FOG policy.
(2) No permittee shall discharge grease in excess of 100 mg/l to the sanitary sewer collection system or contribute to increased downstream maintenance of the sanitary sewer system, or contribute to downstream backups or overflows due to grease blockages as determined by the utility staff. If such discharge occurs, the customer or establishment shall be considered in violation of this permit and subject to the remedies described herein.
(3) No permittee shall contribute or cause to be contributed into the grease interceptor or the sanitary sewer system any of the following:
(a) Hot water running continuously through grease interceptor;
(b) Concentrated alkaline or acidic solutions;
(c) Concentrated detergents, emulsifiers, de-emulsifiers, surface active agents, enzymes, degreasers, solvents or any type of product that will liquefy grease interceptor wastes;
(d) Any substance that may cause excessive foaming in the sanitary sewer system;
(e) Any substance capable of passing the solid or semi-solid contents of the grease interceptor to the sanitary sewer system;
(f) Hazardous wastes including concentrated cleaners, pesticides, herbicides, paints, solvents, gasoline or other petroleum products; or
(g) Waste fats, oils and grease not generated as part of the wastewater system.
(I) Penalties and fees.
(1) When FOG policy violations are found at a permittee’s establishment, the utility may take enforcement action to correct the issue. Violations may be as a result of on-site inspections by utility or the County Health Department personnel, general complaints, consumer tips or observation of collection system problems from various utility department personnel.
(2) A permittee found to be violating the FOG policy shall be sent a notice of violation (NOV) that will outline the nature of the violation and the corrective measures that need to be taken along with a time frame in which the establishment must act. Failure to address the issue, failure to respond or failure to meet the stipulated time frame(s) will result in the issuance of a monetary penalty.
(3) The permittee shall also be responsible for reimbursing the utility for all costs incurred by the utility associated with the violation of the FOG policy, including, but not limited to, collection system maintenance/cleaning costs, property damage, administrative costs, engineering costs and legal costs.
(J) Reporting requirements.
(1) A copy of the information required in the maintenance log, including trip tickets or manifests, must be submitted to the Utility Office when requested by the utility. The report shall be submitted to the Utility Office within 30 days of the utility request for the information.
(2) All reports and correspondence pertaining to this permit shall be submitted to the following address:
WWTF Supt. Town of Newburgh Utility Office PO Box 10 Newburgh, IN 47629 |
(Ord. 2012-20, passed 8-22-2012)