Local requirements are provisions that exceed the requirements of International Building Code (IBC) and International Fire Code (IFC) for the purpose of the protection of life, property, and assets of all parties involved including the building and property owners, employees, and first responders.
(A) Fire protection.
(1) Growing facilities/grower, processing facilities/processor, safety compliance facilities and microbusinesses shall:
(a) Be located only in a standalone, single occupancy buildings and shall not share a building with any other related or non-related business.
(b) Be completely suppressed with a fire sprinkler system that complies with NFPA 13.
(c) Have an FDC located on the side of the building facing the road. There shall be a fire hydrant within 50 feet of the FDC on the same side of the road and or any driveways so that a supply line from the fire hydrant to a fire apparatus will not obstruct any other fire apparatus from entering the drive or facility.
(d) Have a monitored fire alarm system that complies with NFPA 72, which provides total (complete) coverage for the detection of smoke and total (complete) coverage of notification applications throughout the building.
(2) Provisioning centers/retailers may be located in multi-occupancy buildings, as allowed under the provisions of City of Burton zoning ordinance.
(B) Access.
(1) All commercial medical marijuana transaction facilities/marijuana establishments shall:
(a) Install a Knox Box located within 10 feet of the main entrance into the building.
(b) Have approved by the Fire Department any gates that may cross access roads to the property or building and a means of access given to the fire department for the purpose of responding to emergencies at the facility whether or not occupied.
(c) Install address numbers on the side of the building facing the road and visible from the road. Numbers shall be at least 6 inches tall and be a contrasting color from the surface they are mounted on.
(C) Hazardous conditions.
(1) Rooms containing fire protection equipment, controls for ventilation equipment, utility controls, and hazardous materials must be adequately marked and identified to make them easily located by firefighters.
(2) Safety data sheets (SDS) shall be located in an organized binder or filing system located inside the building within 15 feet of the main entrance or secured in a weather proof container on the exterior of the building that can be accessed with a key that shall be stored in the knox box.
(D) Carbon dioxide (CO2) enrichment systems.
(1) The storage, use, and handling of carbon dioxide shall be in accordance with IFC and NFPA 55. All equipment utilized in compressed gas systems shall be compatible with the intended gas and use.
(2) Natural gas burners that are utilized to generate CO2 in plant growing applications shall be listed, labeled, and installed in accordance with the manufacturer's installation instructions. Piping systems, combustion and ventilation air and venting for natural gas appliances shall be designed and installed in accordance with approved standards, the International Fuel Gas Code and manufacturer's recommendations.
(3) Where natural gas burners are located indoors for CO2 enrichment or CO2 storage tanks, cylinders, piping, and equipment are located indoors, rooms or areas containing CO2 storage tanks, cylinders, piping and fittings and grow room/areas where CO2 is released and can collect shall be provided with an emergency alarm system that shall comply with the following:
(a) Continuous gas detection shall be provided to monitor areas where CO2 can accumulate. Detection equipment shall be provided to indicate CO2 levels in each grow cultivation area/room and interior CO2 storage location. Detectors shall be:
1. Listed or approved devices.
2. Permanently mounted.
3. Installed at a height of no more than 48 inches above the floor.
4. Directly connected to the building electrical supply and fire alarm systems and protected from accidental disconnect or damage.
5. Auto calibrating and self "zeroing" devices are not permitted unless they can be zeroed and spanned.
6. Located within manufacturers’ specified detection range for each point of use and storage location.
(b) Activation of the emergency alarm system shall initiate amber strobes and audible horns provided in the vicinity of each interior storage container, cylinder or tank, at each point of release, and where CO2 can accumulate. Additional amber strobes and audible horns shall be placed at entrances to below grade locations and confined spaces. The notification devices shall be rated a minimum of 80cd for visible effect and 75 dBA for an audible effect and shall be mounted in accordance with NFPA 72 requirements. Provide audible visual notification devices at the following locations:
1. Inside an interior storage room / area and outside the room / area at each entrance.
2. Inside grow cultivation room / areas.
(c) Local alarm set points shall be set at 5,000 PPM - Latching alarm as follows:
1. Visual and audible notification in approved locations at room or area in alarm.
2. Activation of automatic system shut off valve.
3. Activation of the automatic natural gas control valves to each burner to a closed position stopping the generation of CO2.
4. Evacuate the room and contact a qualified service company to investigate and address the condition.
5. Reset of the emergency alarm to be conducted by qualified personnel.
(4) Signage shall be required adjacent to each horn/strobe as follows:
(a) Storage area / room: "DO NOT ENTER WHEN LIGHT IS FLASHING - CARBON DIOXIDE LEAK DETECTED"
(b) Grow cultivation room / area dispensing: "FLASHING LIGHT MEANS CARBON DIOXIDE LEAK DETECTED - EVACUATE ROOM"
(c) Entrance to below grade location: "DO NOT ENTER WHEN LIGHT IS FLASHING - CARBON DIOXIDE LEAK DETECTED"
(d) The sign shall have a minimum 1-inch lettering with a minimum ¼-inch stroke. The sign shall be on a contrasting surface of black on yellow and shall be of durable construction.
(e) Signage on the entrance doors to grow, cultivation, and storage rooms shall be provided as below:
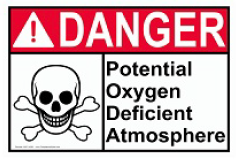
(5) A minimum of 1 portable CO2 meter shall be in use during business hours.
(E) Carbon monoxide (CO) detection.
(1) CO gas detection shall be provided to monitor products of combustion continuously. Detectors shall be:
(a) Listed or approved devices.
(b) Permanently mounted.
(c) Installed per manufacturer's recommendations and directions.
(d) Directly connected to the buildings electrical supply and fire alarm system and protected from accidental disconnection or damage.
(2) CO detection shall be set at 35 PPM and upon activation shall initiate the following:
(a) Close the automatic valve to each burner.
(b) Activate the mechanical exhaust system.
(3) All CO2 burner systems shall shut down in the event of a loss of electrical power to the CO detectors.
(4) A minimum of 1 portable CO meter shall be in use during business hours.
(Ord. 2017-92, passed 12-18-2017; Ord. 2019-92, passed 1-14-2021)